The Irish heat pump market is rapidly expanding due to climate change awareness, EU CO2 reduction goals, and Ireland’s alignment with other EU members. Heat pumps are increasingly seen as a key solution, particularly with Ireland’s growing renewable energy from wind and photovoltaics. Despite this growth, there’s a lack of in-depth understanding of heat pump technology among the public, professionals, and renewable energy companies.
From our Irish distributor Master Therm Ireland / Lukas Kadlik
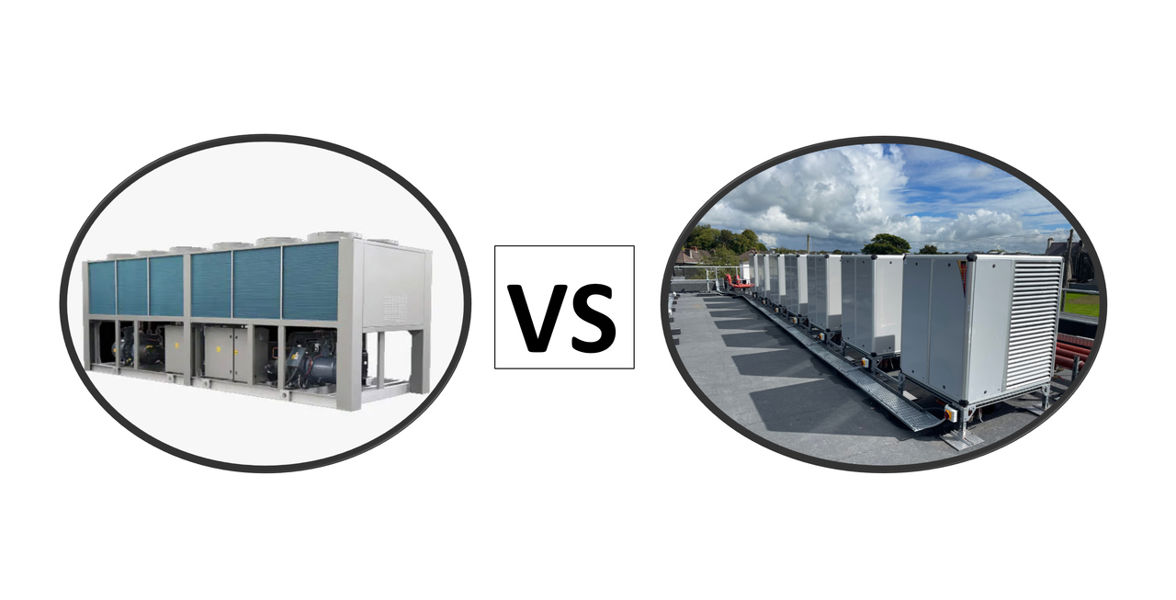
The Irish heat pump market is rapidly expanding due to climate change awareness, EU CO2 reduction goals, and Ireland’s alignment with other EU members. Heat pumps are increasingly seen as a key solution, particularly with Ireland’s growing renewable energy from wind and photovoltaics. Despite this growth, there’s a lack of in-depth understanding of heat pump technology among the public, professionals, and renewable energy companies.
Comparing to other EU countries, especially those with colder climates, it’s evident that genuine heat pump technology has been refined over the last two decades. Consequently, authentic heat pump brands are preferred in countries like Sweden, Denmark, Germany, the Czech Republic, and Austria over modified Chillers/Air Conditioning units, which are often initially cheaper but less effective and durable. This trend suggests a need for better education and decision-making in the heat pump market, particularly in understanding the long-term benefits and efficiencies of true heat pump systems over more cost-effective but less efficient alternatives.
Below, we aim to provide key insights that will assist Consulting Engineers in offering enhanced value and more effective long-term heating and cooling solutions to their clients.
System Design for Heat Pumps in Commercial Buildings
For consulting engineers, understanding that the efficiency of heat pump systems in commercial settings depends on several factors is essential. These include the quality of the compressor, expansion valves, heat exchanger sizing, system controls, and, importantly, evaporator size
Traditional chiller systems, sometimes repurposed as heat pumps, are primarily designed for cooling, with an optimal temperature differential between 15 – 20 °C. Adapting these systems for heating in commercial buildings is not their intended use, and such usage can greatly reduce their lifespan.
In contrast, both air-water heat pumps and ground source heat pump systems present more sophisticated systems which can be challenging for commercial buildings. These systems must efficiently transfer heat from the refrigerant to water, and then to the indoor air, often dealing with temperature differentials exceeding 50 °C. This scenario requires components of high quality, precise dimensioning, and advanced control systems, all specifically engineered for heating purposes to ensure efficiency and durability. This distinction is critical for the effective design and implementation of heat pump systems in commercial environments.
Undersized or unsuitable components
For Consulting Engineers, it’s important to understand the limitations of chiller-based systems posing as heat pumps. These systems, often designed for average loads, not maximum, see a significant drop in effectiveness and overall efficiency under higher heat loads, falling short of genuine heat pump performance.
A key issue is the evaporator design, where fin spacing in chiller units (commonly 0.8 – 1.2mm) is much narrower than in true heat pumps. This leads to frequent defrosting, especially in humid conditions like Irish winters, as the small gap clogs quickly with freezing condensate. These units endure more defrost cycles and increased thermal fatigue, reducing the lifespan of the evaporator and compressor.
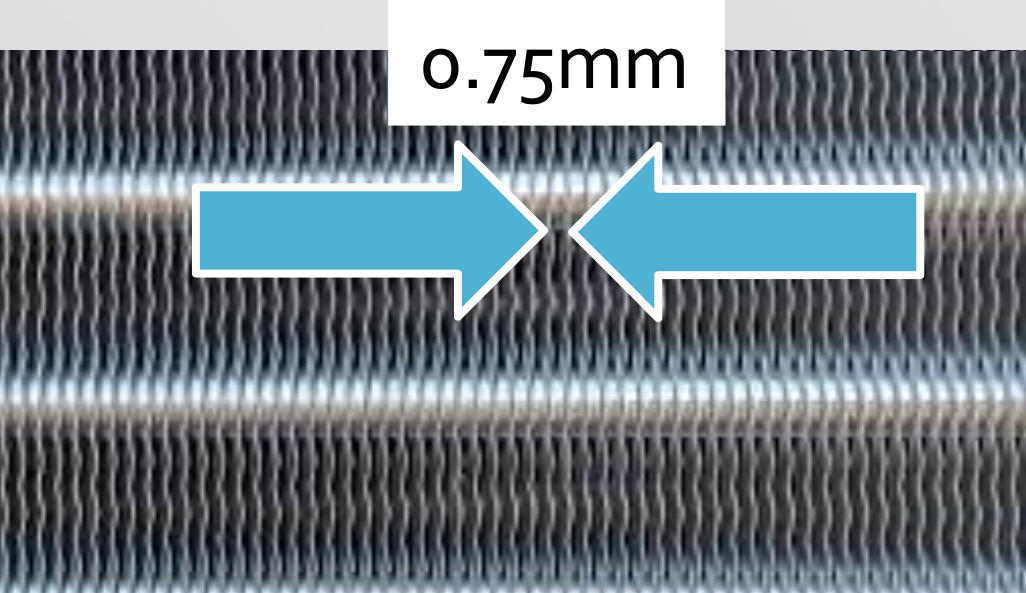
Small evaporator fin spacing
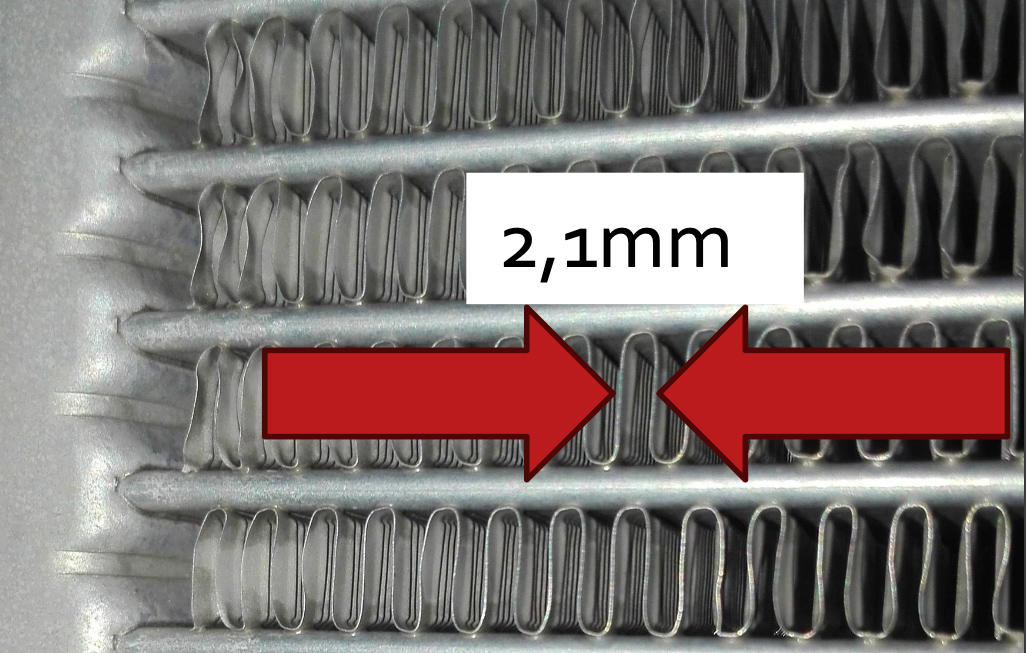
Purpose built heat pump evaporator
From a Manufacturing point of view, adjusting the fin spacing to enhance efficiency and reduce defrosting would require larger evaporators, doubling their height and consequently the unit’s size. This change would necessitate modifications in manufacturing plants and housing, increasing costs in materials, energy, labour, shipping, and storage.
These challenges are among many faced by chiller units modified as heat pumps. While these units may achieve similar COP/SCOP results in laboratory settings, their real-world efficiency and durability are often compromised.
Chillers are not a heating system but a heat source
From a Consulting Engineers’ perspective, it’s important to understand that chillers, often marketed as heat pumps due to their perceived ease of design, are fundamentally different in function. These chillers, despite their potential to match output requirements, are designed primarily as heat sources, not complete heating systems. This distinction has significant implications for system design and overall cost. While Chillers may be a easy one box solution, it often results in troublesome design issues and operation.
In practice, chillers require additional components for a complete heating system, such as bivalent sources, circulation pumps, heating circuit controls, domestic hot water controls, solar panel integration, and weather compensation controls. These additional requirements often negate the initial cost advantage, and responsibility for the system’s functionality and efficiency usually falls on the installer rather than the manufacturer.
Moreover, chillers typically lack the management and regulation (MaR) features necessary for efficient operation in heating applications, especially in commercial settings. They may operate in a simple on/off mode, which is less efficient than the variable output of true heat pump systems.
In contrast, genuine heat pumps come with integrated control systems that are designed to work in harmony with the building’s heating requirements and other heat sources. This leads to higher efficiency and longer lifespan in real-world applications. Therefore, for long-term efficiency and cost-effectiveness, investing in a true heat pump system is often the more prudent choice for commercial heating solutions.
Lifespan of heat pumps
From a Consulting Engineers’ perspective, it’s important to note the significant difference in lifespan between chillers used as heat pumps and purpose-built systems. Chillers which are used as Heat Pumps can have as short a lifespan as 5-7 years due to oversizing, while genuine, correctly designed, heat pump systems have a lifespan of 15-20 years, although this can vary based on usage and application.
The extended lifespan of purpose-built heat pumps is attributed to their robust design, including rust-resistant aluminium or stainless steel frames, water and dust-sealed control compartments, long-lasting evaporator fans, and high-quality inverters. Furthermore, these systems are designed for easy access to all mechanical, electrical, and refrigeration components for maintenance and replacement.
In contrast, chillers, even when labelled as heat pumps, generally lack these features. This disparity in design and build quality directly impacts the longevity and reliability of the system, an essential factor for consulting engineers to consider in their project planning and recommendations.
COP – Coefficient of performance , SCOP – Seasonal coefficient of performance
For Consulting Engineers, understanding the metrics of heat pump performance, like the Coefficient of Performance (COP), is critical. However, it’s important to be aware that the real-world conditions under which these metrics are achieved can vary significantly. For instance, the standard testing condition A7W35 often doesn’t reflect actual operating conditions, and the EN14511 standard allows a 15% range of accuracy. Manufacturers can also manipulate settings like defrost periods to enhance performance figures, leading to results that are more marketable than accurate.
SCOP (Seasonal Coefficient of Performance), governed by EN14825, is a more comprehensive testing method. It considers variables such as water heating temperature, climate conditions, system sizing relative to building heat loss, and other factors.
It’s essential to recognise that the efficiencies declared in manufacturers’ brochures may differ significantly from the actual efficiency when the system is integrated into a heating distribution network. The overall system efficiency, including the plant room, emitters, and controls, is more indicative of performance than just the heat source’s COP/SCOP/SPF.
Therefore, the key to real efficiency lies in the comprehensive design of the heat source in conjunction with the entire heating system, including a quality control system and an appropriate control strategy. This holistic approach is crucial for Consulting Engineers when designing and planning heating solutions.
Summary of steps how to differentiate Chillers / modified AC units from purpose-built Heat Pumps
For Consulting Engineers, distinguishing between genuine heat pumps and Chillers / modified air conditioning (AC) units is crucial. Here’s a summarised guide:
- Technical Specifications: Review the product’s technical list or data plate. If the outdoor unit is referred to as a “condenser” instead of an “evaporator”, it’s likely a modified AC unit.
- Evaporator Fin Spacing: Check the spacing of the evaporator fins. Spacings under 2 mm typically indicate an AC unit.
- Size of the Outdoor Unit: Assess the overall physical size. Compact units are unlikely to meet the minimum spacing requirements for genuine heat pump evaporators. Compare the size of the unit to the manufacturer’s standard AC units to check for consistency.
- Service Access: Examine the accessibility of mechanical parts. Restricted access usually signifies a shortened lifespan, common in modified AC units.
- Laboratory Test Reports: Investigate the availability of official test reports. A manufacturer’s reluctance to provide these reports can imply lower real-world efficiencies than advertised.
- Control System and Integration: Determine if the heat pump includes a comprehensive control system, potentially with a built-in bivalent source and compatibility with other heat sources like solar panels. AC units, typically designed for cooling, rarely feature these integrations.
These steps are essential for making informed decisions in your sustainable and renewable energy projects, ensuring the selection of appropriate and efficient heat pump systems over Chillers / modified AC units.
Purpose-built Heat Pumps combined with correctly designed system controls, is the only way to successfully achieve performance and efficiencies crucial for meeting the sustainable energy targets.
Lukas Kadlik and The MasterTherm Heat Pump Team
Sustainable Energy Authority of Ireland (SEAI) Engineers Ireland Master Therm Heat Pumps / tepelná čerpadla MasterTherm Ireland
Courtesy of Master Therm Ireland / Lukas Kadlik – www.mastertherm.ie